Sign up here to subscribe to the Grower2grower Ezine. Every two weeks you will receive new articles, specific to the protected cropping industry, informing you of industry news and events straight to your inbox.
Aug 2022
Converting a coal fired boiler to run on biomass

Thymebank’s Leanne Roberts explains the process for their greenhouse lettuce and herb growing operation in Marlborough
Leanne Roberts, Director of Thymebank has recently presented in regards to her company’s conversion from coal to biomass. With the help of EECA this has been achieved although there have been twists and turns to navigate during the process.
-
A brief history of the business
We purchased the business in 2013. We run a spray-free operation harvesting, packaging and dispatching fresh salad and herb products from an area of 5,500m2. We have eight employees.
-
When/how/why did you begin the transition process from coal to wood chip
We began in March this year. Prompted by the increase in ETS, notification of our coal supply not being available and the opportunity work with EECA motivated us to bite the bullet and convert.
-
What technology have you implemented
We have converted our boiler to run on biomass- we have been working with a local arborist and some nut growers to take their waste products (wood chip and nut shells)
-
How have you sourced your woodchip?
This was in partnership with a local arborist (could you expand). When exploring what fuels we could use to run our boiler our first conversations were with our boiler manufacturer. Working closely, we were able to understand the opportunities, possibilities and requirements each alternate fuel could offer. Our operation also wanted to find an alternative fuel that was clean, and utilized something from a waste stream.
We investigated wood pellets and woodchip. We wanted to know our fuel was as clean as we could get it, which is why we started looking more closely at wood chip. When looking at commercial supply of woodchip, we were mindful that if there was a shortage, we could be vulnerable to shortages. We also recognized that some commercial woodchip is not a waste product, but a product in its own right.
We then approached a local arborist about what they do with their woodchip and the project has evolved from here.
We have since spoken with local nut growers and are using their nutshells mixed in with the wood chip which seems to be successful.
-
What type of woodchip/size are you using (and how is this dried)?
We are using wood chip from the arborist which is made up from a variety of sources (depending on their work) We are working on refining the drying process and are looking to increase our storage onsite so we can dry out and blend our fuel sources.
It is critical that we are able to source fuel throughout the year and mix it onsite to ensure we have better control.
We are also working with local nut growers who have a waste product (nutshells). The nutshells have a much better calorific value and are working well when blended with woodchip.
-
What is the calorific value of the woodchip compared to coal?
As a % comparison
- Calorific value of pine nut shells is about 22%
- Calorific value of woodchip is 15%
- Calorific value of coal is 42%
Image: Pine and Hazelnut shells a waste product that have a high calorific value.
-
What has been the cap ex required to change/alter your systems
So far, we have spent $25,000 on the change. This has included covering our fuel storage area. We have identified that we are best to build a larger fuel storage area and will look to do this before next winter.
-
What is the comparison in op ex required?
We have found that including ETS, coal is now completely uneconomic to run. Biomass will be more cost effective and we are pleased to have had the help to convert our boiler.
-
How has EECA helped with the project?
Insa Errey from EECA has been really supportive and helpful putting us in touch with good people to check and run our decarbonization plans with. They have offered some funding towards our conversion and are interested to see how our approach to sourcing an appropriate biomass to run as fuel progresses.
-
Please explain the difficulties associated with gaining consents/ RMA constraints etc.
We have been thinking about this conversion for many years. It was one of the first things that was on our list of things we wanted to change about the business. However, we found the process of selecting an alternative way to heat the site really challenging with many different advisers and experts giving us a wide range of options, all which were unaffordable. Working with our boiler manufacturer, we got a greater understanding of our options and since the boiler is only used for such a short period of time, conversion was the best option.
We have found making our own decisions has been straightforward – we can gather information and identify, with the help of people such as our boiler manufacturer, an appropriate fuel. We have found working with EECA to be so helpful and they are a very supportive agency. EECA have been great to connect us with technical experts and provide information so we can develop and action our business decarbonization plan. We have been working with our Resource Management consultant who is fantastic and really experienced with resource consent in our area. We are waiting on our consent for the conversion. Our local Council are requiring a lot of information to verify why biomass – including woodchip, is a better option than coal. It seems to be a quirk of the consenting process.
It would be great if there was an ability to have a consenting pathway for businesses and groups who are converting away from coal to a less harmful fuel such as biomass. There will be many operations, not just in our industry, making significant changes and embarking on their own decarbonization plans in the near future. This should be something that is addressed or made into a consenting pathway.
-
Are you able to measure the reduction in ETS cost on your business due to this transition?
We will immediately see a reduction in ETS as there will be no ETS paid on biomass as there is with coal.
-
Who has been in charge of the project implementation?
My Dad (Marc Roberts) has really been driving the project. By nature, he is quite a methodical person. He has been working through and researching fuel types, speaking with technical advisers and coordinating the expertise needed to complete the conversion. It was Dad’s idea to work with a local arborist and he has been doing research into the different fuel options such as nutshells. This has been a real passion project and we have been very lucky that Marc has been able to put the time into managing the conversion.
We have had many hours (especially my Dad), spent out at site looking at the boiler, inspecting and working with tradespeople. He has even been out testing the moisture levels of the biomass and devising plans to increase our onsite fuel storage.
Image above the blended woodchip, hazle and pine nut mix.
Cover Image above of Marc Roberts inspecting the woodchip.
Article written and compiled by Stefan Vogrincic
All Article’s checked and edited by Marie Vogrincic
I appreciate your comments. Please feel free to comment on the grower2grower Facebook page:
https://www.facebook.com/StefanGrower2grower/
CLASSIFIED
Photo
Gallery
Subscribe to our E-Zine
More
From This Category

New Industrial Process Heat Consenting Requirements in Aotearoa New Zealand
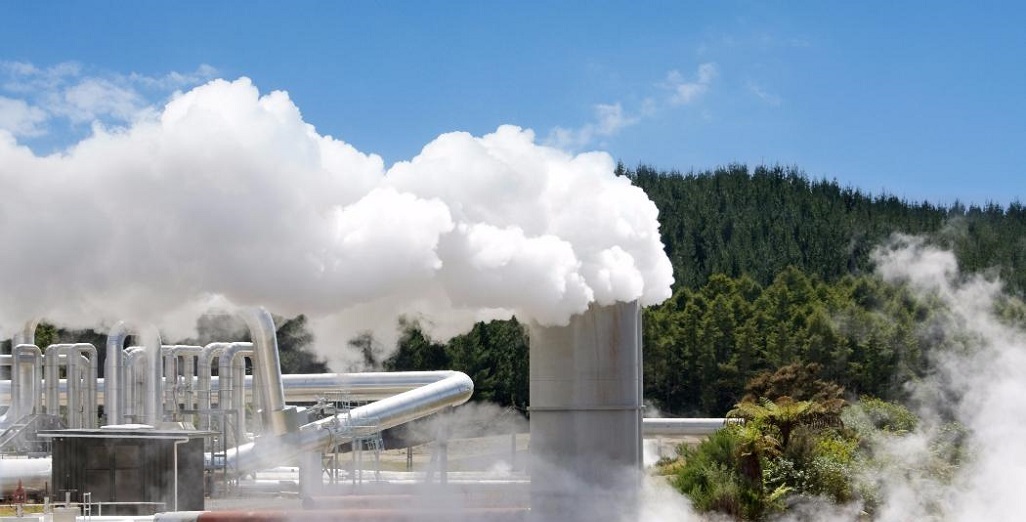
GNS Scientist wants greenhouse grower to consider geothermal Heat
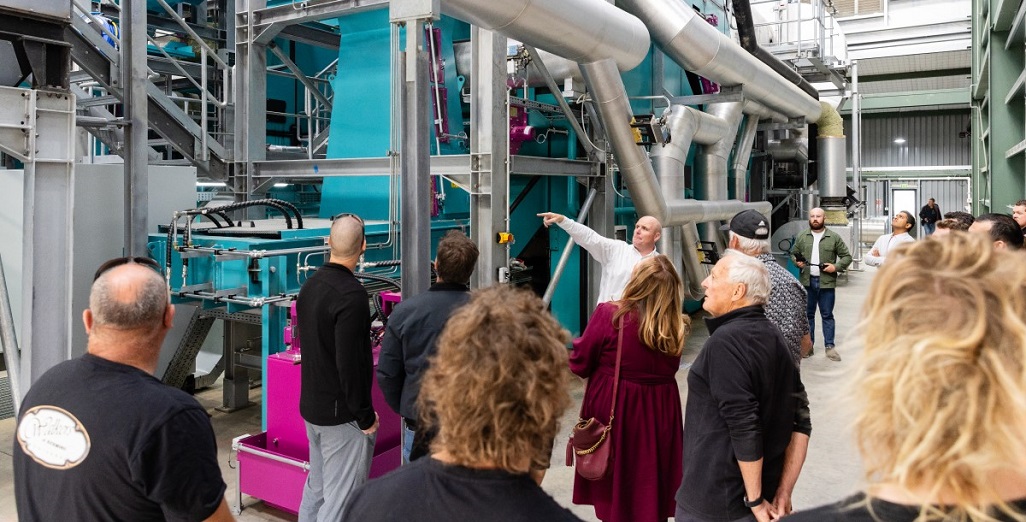
Ribbon cutting marks the opening of a new JS Ewers Biomass Energy Centre
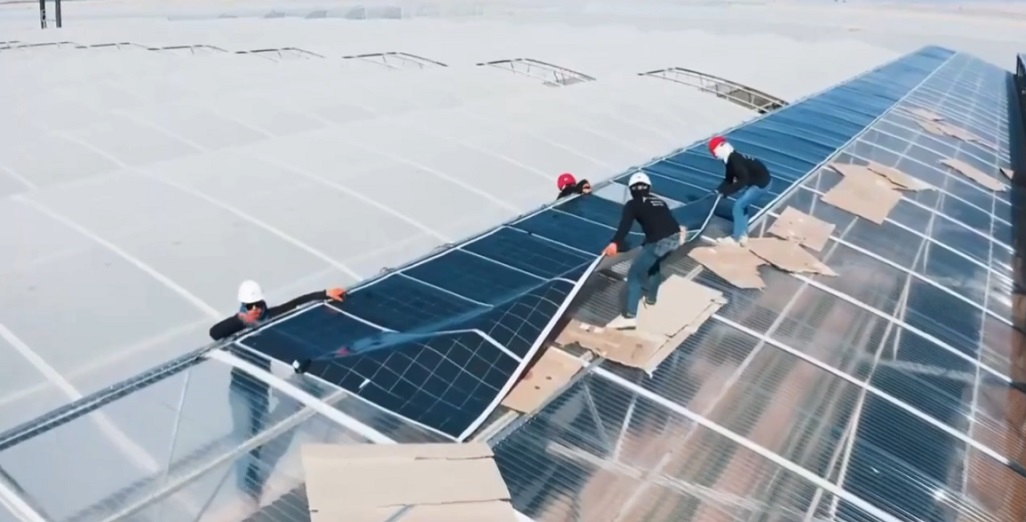
Flexible Solar Panels Look Set to Disrupt the Industry
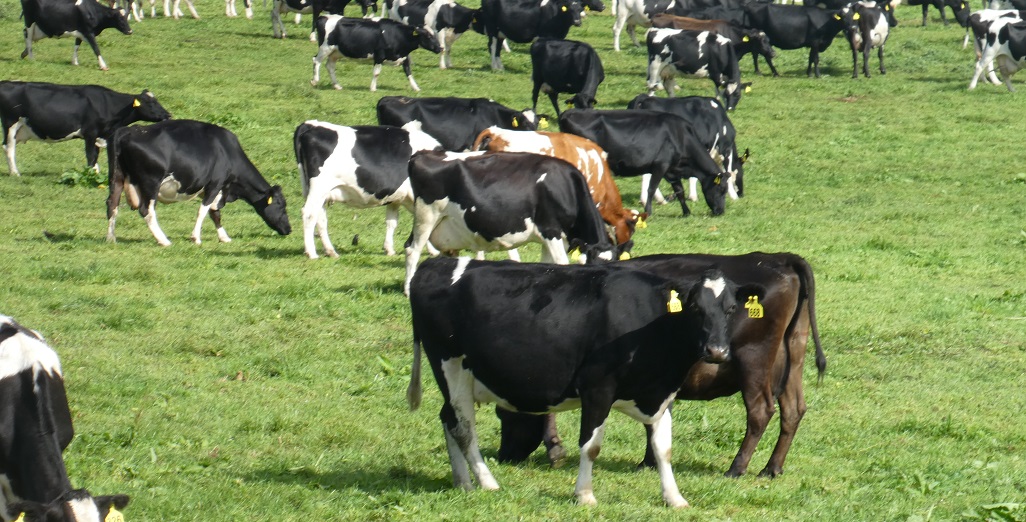